OUR CORE SERVICES
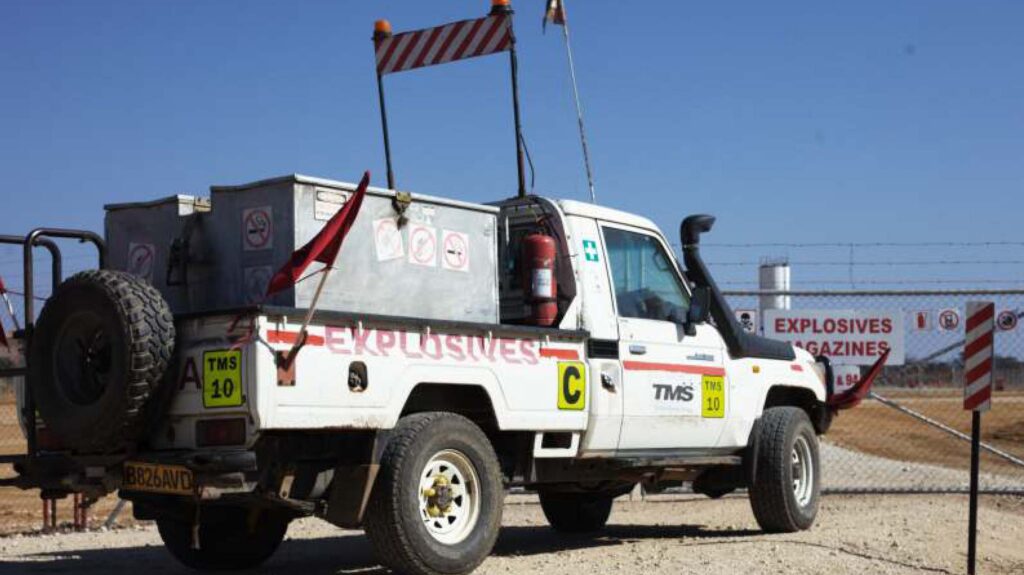
TMS supplies the full range of BME blasting products in Botswana
TMS delivers a wide range of service packages that deliver real quantifiable value through optimal blasts by leveraging BME’s knowledge base and best in class technology, products, and equipment. Additional customised services are available to meet unique local customer requirements.
DOWN THE HOLE (DTH)
TMS DTH service delivers INNOVEXTM, our high quality, reliable bulk emulsion explosives, to blast holes, using BME’s mobile manufacturing units (MMU). We ensure fit-for purpose products are pumped to achieve improved and consistent fragmentation.
Clients can also make use of extensive range of initiating systems and the market leading AXXISTM electronic detonation system. Blast quality can be further enhanced by using BME’s BLASTMAP IIITM software.
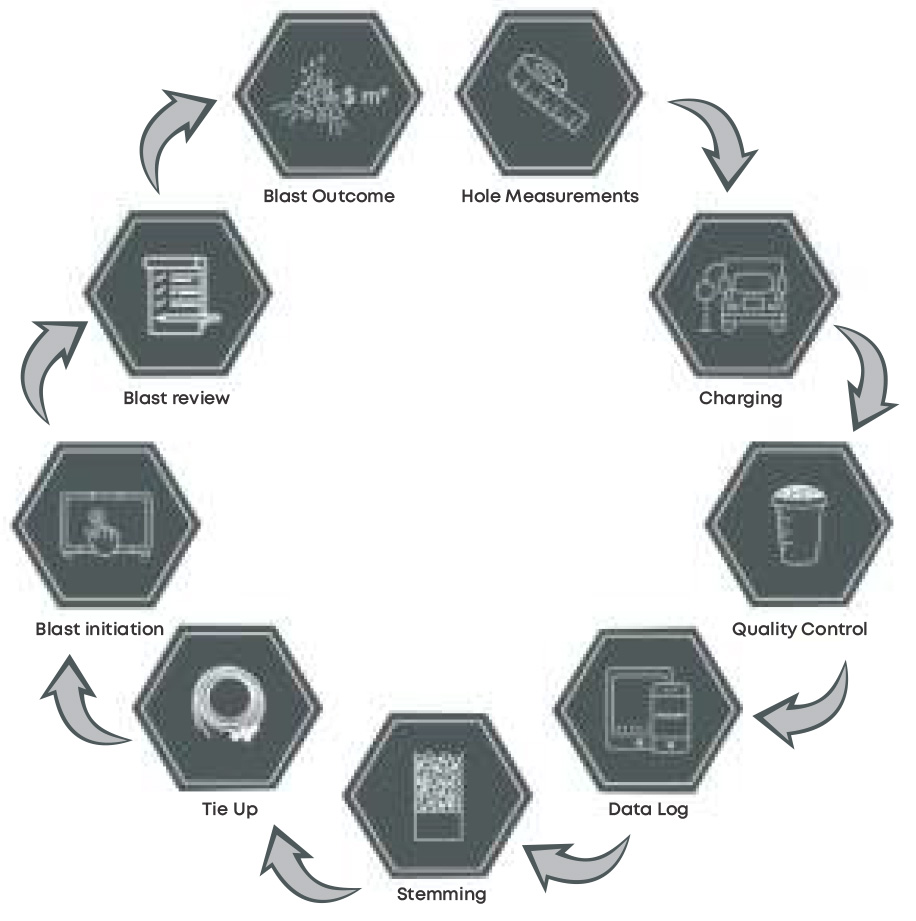
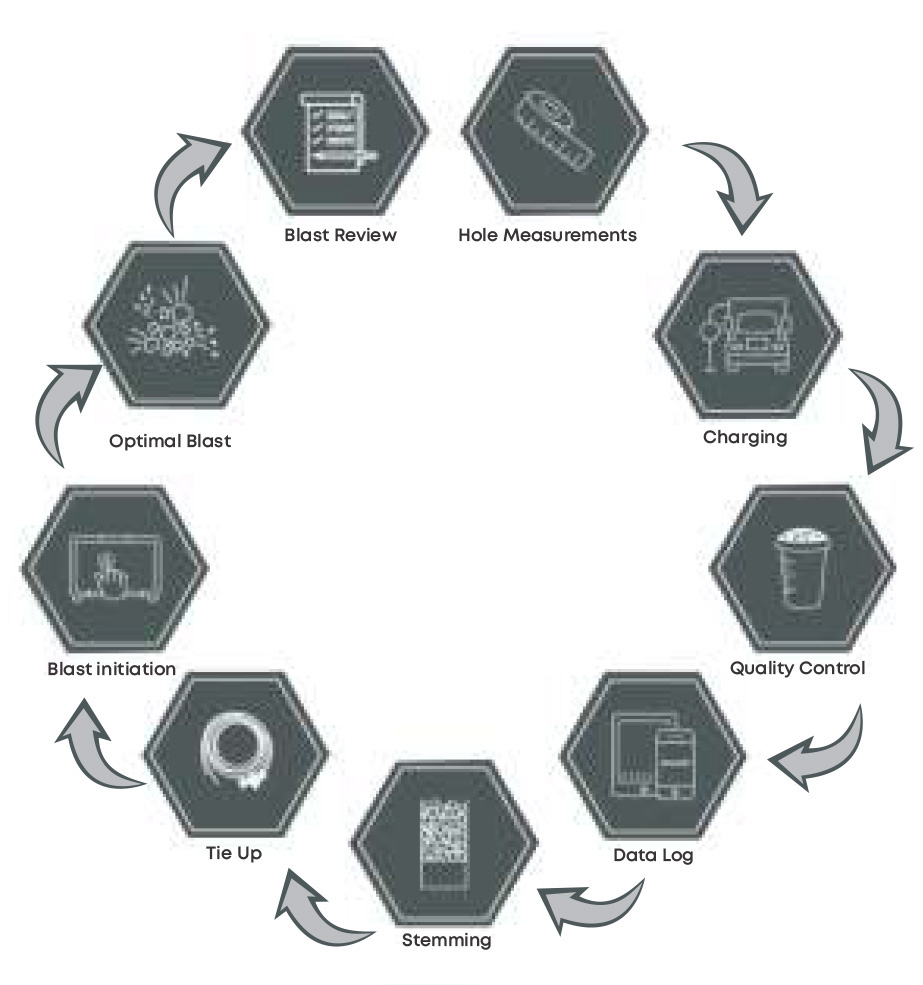
PRIME, LOAD, TIE, AND SHOOT (PLTS)
TMS’s PLTS service is designed for customers who require TMS’ team to perform a full blasting service. This service ensures that skilled resources
are available to the customer to achieve the best blasting results.
This service option is ideal for companies whose core business is not blast planning and execution. TMS takes on the responsibility for the full operation, safety, and management of the blast service.
ROCK ON GROUND SERVICE (ROG)
In this comprehensive service to the client, TMS takes full responsibility from blast design to analysing fragmented rock (excluding drilling), allowing the client to outsource this function with value being measured on fragmentation quality and volume of broken rock.
We provide the materials, equipment and skilled staff required to deliver cost-effective and quality blasting, allowing the client to focus on their core business
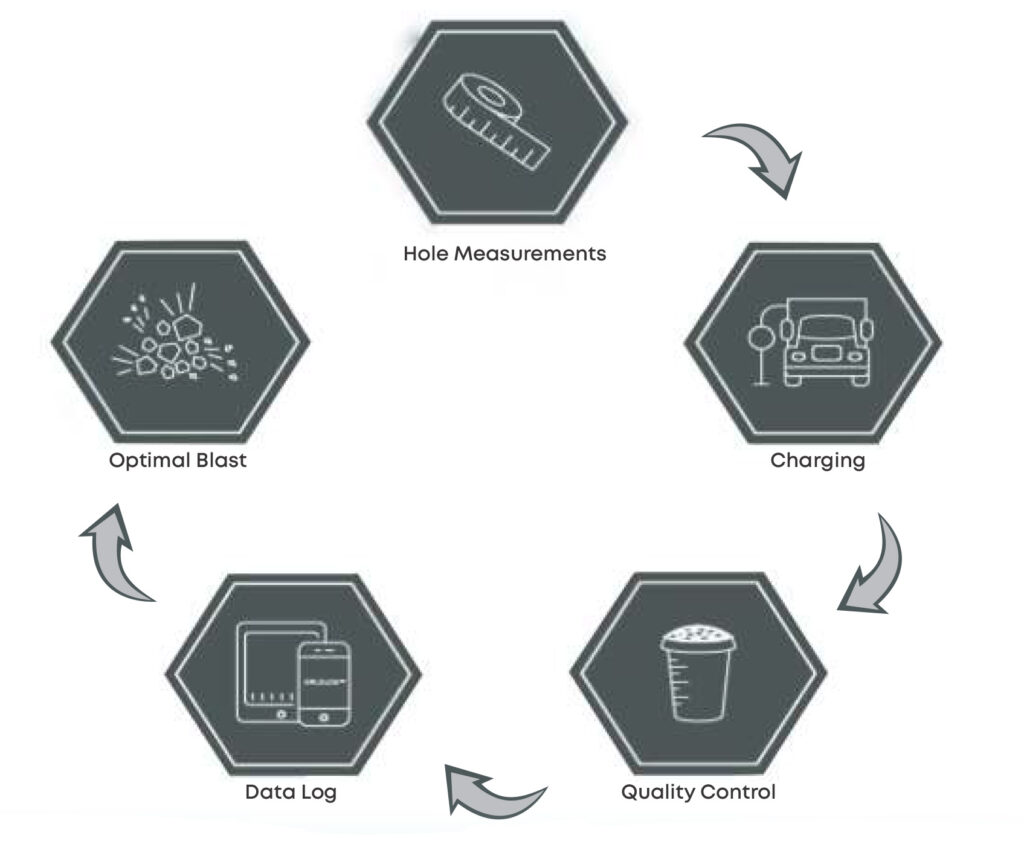
MINE TO MILL OPTIMISATION
TMS’ exclusive M2M service offering delivers the full range of benefits across the mining value chain. Blast designs can be optimised to achieve required fragmentation, blast movement, and muckpile shape, delivering improved loading, crushing, and milling rates. M2M will reduce overall mining costs by ensuring that downstream productivity is increased.
The customer can be assured that the professionals who design the blasts and those who apply the designs in the field will be competent and fully conversant with the project requirements. Benefits include closer management of downstream costs and overall systems optimisation, offering a cradle-to-grave view of the entire mining process in consultation with mine and plant personnel.
TMS’ exclusive M2M service offering delivers the full range of benefits across the mining value chain. Blast designs can be optimised to achieve required fragmentation, blast movement, and muckpile shape, delivering improved loading, crushing, and milling rates. M2M will reduce overall mining costs by ensuring that downstream productivity is increased.
The customer can be assured that the professionals who design the blasts and those who apply the designs in the field will be competent and fully conversant with the project requirements. Benefits include closer management of downstream costs and overall systems optimisation, offering a cradle-to-grave view of the entire mining process in consultation with mine and plant personnel.
FOUNDATION FOR STRONG PARTNERSHIPS
TMS delivers real, quantifiable value through the application of best-in-class technology, products, and services that ensure a consistent user experience and improved product performance. TMS’ flexibility in the mobile manufacturing facilities for emulsion products places it in a strong position to reach new markets and to add value to customers in any region. Our procurement strategy leverages both local and global sources, adding to the efficiency.
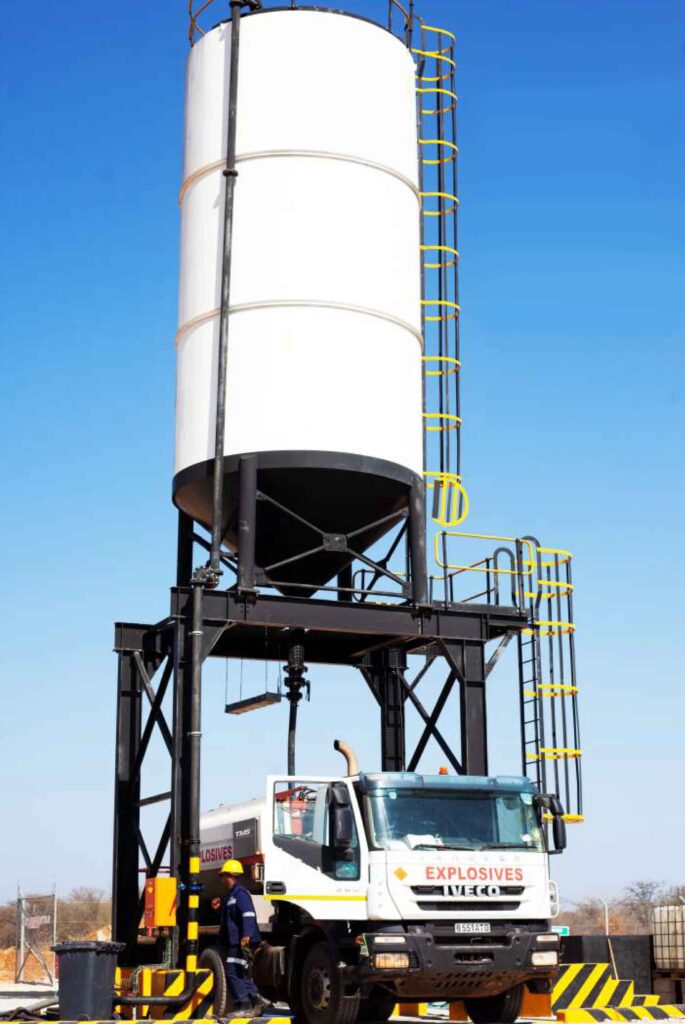
SAFETY
Continued focus on safety through enhanced management and improved safe operational processes.
EMPOWERING
Empowering and up-skilling the workforce to address the skills shortage in the mining industry.
SAVE COSTS
Identifying synergies, efficiencies, and opportunities to save costs with strategic partners and clients, especially as increasing costs place pressure on the sustainability of mines.
SERVICE EXCELLENCE
Driving partnerships from the point of view of supply chain management, innovation, and service excellence.
SOCIAL RESPONSIBILITY
We’re committed to reducing our effect on the environment, from recycling used oil to minimising our carbon footprint by fitting technology to our plants to reduce greenhouse gases. We partner with communities to this effect and empower our employees on the same.
TECHNOLOGY
Leveraging the power of digital technology to drive operational and service excellence.
BUSINESS MODEL
Continued improvement of the business model to ensure that customers always find it easy to do business with us.
TMS is the exclusive distributor of BME explosive products in Botswana. BME products are market leaders in safety innovation and have been in the market for over 40 years.
TMS supplies the full range of BME blasting products in Botswana
1. Bulk emulsions
2. Packaged explosives
3. Initiating systems
4. Electronic detonators (AXXIS TM)
5. So ware for computers, tablets and smartphones
6. On-site bulk emulsion plants
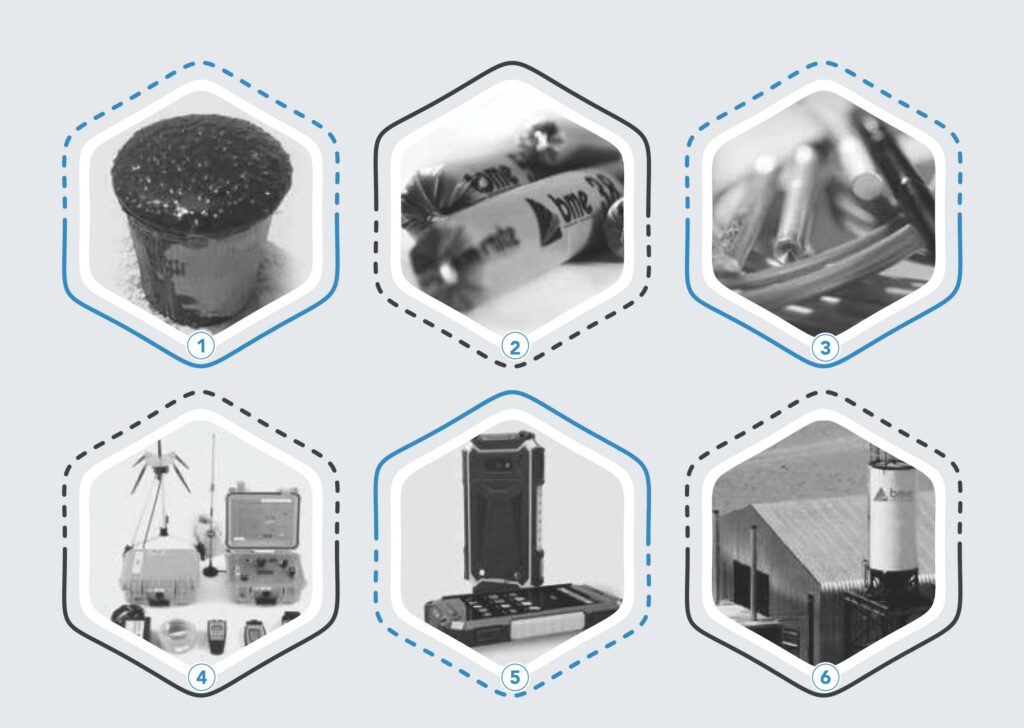
EMULSION DELIVERY
TMS has a variety of manufactured equipment for surface and underground operations and is committed to R&D with i’ts technology partners to develop better and more cost-effective blasting solutions.
Su rface Equipment
Su rface Equipment
To deliver our products efficiently and cost-effectively in the opencast environment, we have developed a range of fit-for-purpose equipment.
Mobile manufacturing units (MMUs) – BME assembles a range of emulsion and heavy ANFO MMUs for TMS, which cater for all surface mining and quarrying applications.
Stemming trucks – TMS provides a stemming plant fitted on an Iveco 380 T42 WH 6×6 cab chassis, or chassis specified by the client. The stemming truck is capable of delivering 15-18 cubic meters of crush aggregate per load.
Cruiser charging unit (CCU) – TMS’ CCU is a compact charging system available for use with BME’ emulsion formulations for surface and underground.
Bulk technical support vehicle – This vehicle is fitted on a 4.2 l 4×4 Toyota Land Cruiser and is fully equipped to provide technical and monitoring capabilities, to enable operations to optimise their blasting.
Modularised emulsion plants – TMS’ plants are designed to be mobile, robust, and userfriendly, making them ideally suited for the mining environment. TMS provides a range of manufacturing capacities to suit customer demand as well as any other blast management related infrastructure such as storage, containerised offices, and technical equipment.
Underground Equipment
To make emulsion systems available throughout all underground operations, TMS & BME have developed an in- house range of emulsion pump technology.
Vertical emulsion pipeline – Designed to improve logistical efficiencies in the transportation of explosives to underground operations, BME’s emulsion pipeline delivers emulsion vertically from surface to underground storage tanks.
Underground filling stations – Designed to operate in conjunction with Portable Charging Unit (the Mini- Charger). These filling stations are permanently located near the entrance to operating sections.
Emulsion charging units (ECUs) – These can be fitted to a wide range of underground mine carriers and are ideal for large trackless operations, where extensive quantities of emulsion are required for each blast.
Maxi-Charger (rail-bound) – The MaxiCharger is a compact charging system developed for use with emulsions and is designed for track-bound development operations.
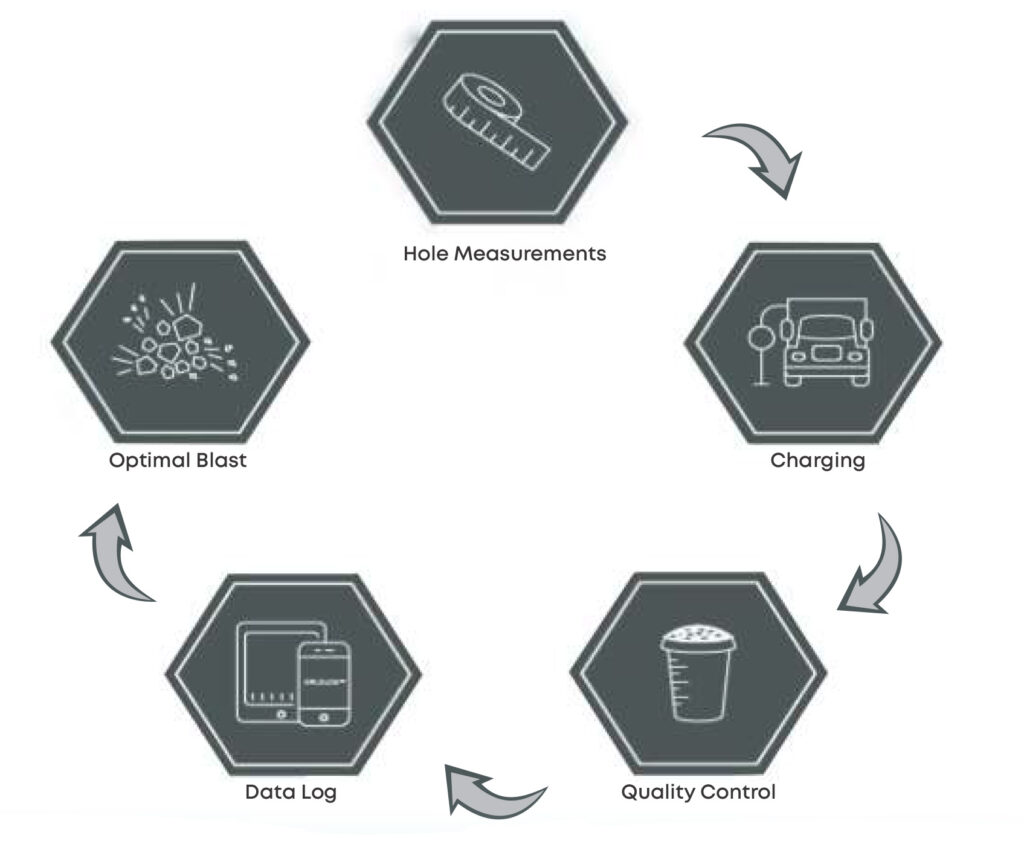
Mega-Charger HP1500 and LP1500 – This purpose-built charging unit is designed for reduced capital outlay and is available in both low-profile and high-profile designs in mechanised underground mining operations.
Uphole Charging Unit or Mega-Charger Uphole – The new range of Uphole Charging Units have been designed for underground massive mining operations, which use uphole blasting practices.
Mini-Charger portable charging unit (PCU) – This PCU represents the forefront of pumpable emulsion technology available for use in narrow orebody mining operations. The PCU is manufactured for rough underground conditions,but is light and compact enough to be carried into stopes by mine personnel.
Maxi-Charger – This has been designed for rapid reloading in large development and stoping faces. The high strength pump allows for longer hose lengths and can connect up to six emulsion bags at a time.